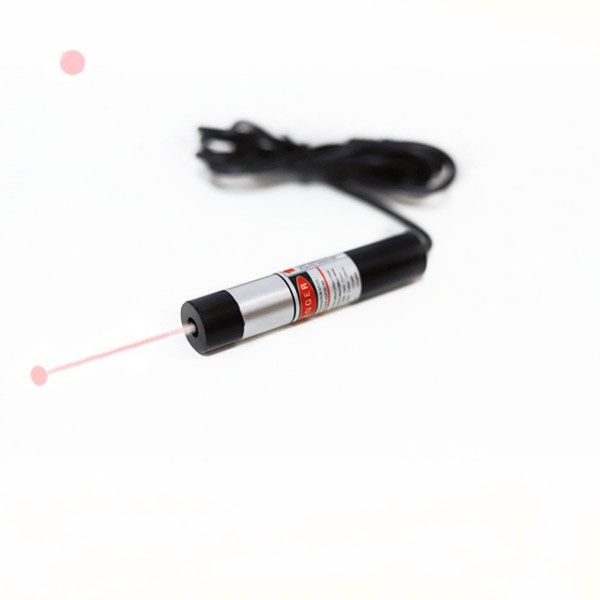
Infrared laser modules have got a lot of advantages and good industrial adaptability in the industrial field. It generates high directivity infrared laser beam emission and maintains a concentrated IR beam during long distance transmission. In industrial positioning system, it can help operator make accurate indicating of the target position with minimal error with low energy dispersion. Usually it gets special design of adjustable focus lens, after high energy concentration on a small spot, it is able to be used high efficiency and high quality raw material processing works, including laser welding, laser cutting work etc.
After connect with AC/DC adapter, 795nm infrared laser diode module emits a single wavelength of 795nm IR laser light with a narrow spectral width, and less effect by ambient light. After its proper use of electric power source with correct operating voltage, on the basis of its good monochromaticity, it can be used for accurate spectral analysis and color recognition so as to improve detection accuracy for industrial inspection. Owing to its noncontact infrared laser light source generation, the real raw material processing work gets no contact with object during processing or detection, avoiding contact measurement or processing to damage the surface of the object. It is suitable for fragile, deformable or surface-demanding workpieces.
Industrial adaptability:
Strong environmental adaptability: The 795nm infrared laser diode module can work stably in a wide range of temperature and humidity, and has a certain resistance to dust, oil, etc. For example, in harsh environments such as foundries, it can still be used for infrared dot positioning and detection despite dust and high temperature.
Easy to integrate: Being made with small size and light weight, 795nm infrared laser is easy to integrate into various industrial equipment and automated production lines, which can be flexibly installed in different positions. Cooperating with robotic arms, conveyor belts and other equipment, it can achieve automated operation.
Controllable precision: By controlling the parameters of the 795nm infrared laser diode module and coordinating with high-precision optical components and control systems, micron-level or even higher precision positioning and processing can be achieved so as to meet the needs of precision industrial production.
High safety: 795nm infrared laser is invisible IR light, which is relatively less harmful to human eyes, and safety protection devices such as light curtain sensors and guardrails can be installed to further improve safety in industrial production.
Applications:
Precision machining: In the microelectronics industry, 795nm infrared laser can be used micron-level marking, cutting, welding and other operations. Featured by high energy density and ultra fine IR dot diameter, it can achieve high-precision machining on tiny electronic components, improving production efficiency and product quality.
Positioning and calibration: In automated production lines, it can be used for workpiece positioning and assembly calibration to ensure the accuracy and consistency of the production process. For example, in the fields of automobile manufacturing and machinery manufacturing, it provides accurate position references for robots, helps robots achieve autonomous navigation and precise grasping, and improves production efficiency and flexibility.
Measurement and detection: 795nm infrared laser light source can be used to measure parameters such as length, angle, shape, etc., providing strong support for product quality control. In industrial detection, such as material surface defect detection, crack detection, etc., its good IR laser beam quality can clearly show tiny defects on the surface of the material.
Laser heating: 795nm infrared laser diode module can be used as a point-focused heating source for local heating treatment of materials. For example, in metal heat treatment, the high energy generated by the laser is used to quickly heat the surface of the workpiece and quickly quench it. By precisely controlling the laser energy and action time, precise control of the heating area and temperature can be achieved.